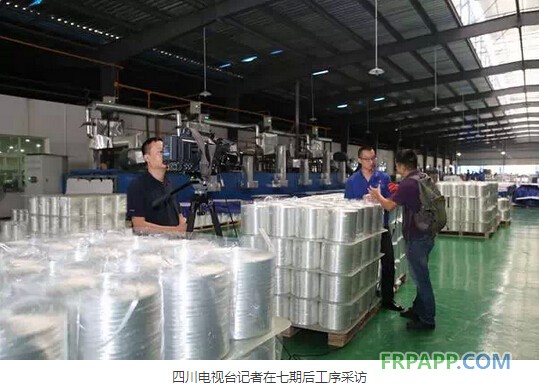
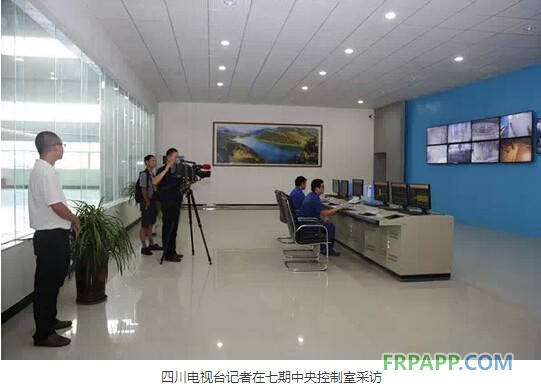
2014年,七期池窯認(rèn)真貫徹落實(shí)職代會(huì)精神,克服了宏觀經(jīng)濟(jì)持續(xù)低迷,市場(chǎng)形勢(shì)整體嚴(yán)峻的不利局面,全體干部員工齊心協(xié)力,頑強(qiáng)拼搏,大力倡導(dǎo)和踐行適應(yīng)時(shí)代發(fā)展的經(jīng)營(yíng)管理理念,在加強(qiáng)隊(duì)伍建設(shè)和管理的同時(shí),努力挖掘最大潛能,率先試點(diǎn)推行新的工藝技術(shù),使得拉絲作業(yè)率得到大幅度增長(zhǎng),成為威玻池窯生產(chǎn)線(xiàn)的又一標(biāo)桿企業(yè)。
日常工作中,該公司將“精、細(xì)、實(shí)”貫穿到整個(gè)管理流程,通過(guò)不斷學(xué)習(xí)交流,大膽探索,創(chuàng)建了具有自身特色的管理模式。出臺(tái)行之有效的績(jī)效考核辦法,強(qiáng)力推行全面預(yù)算管理,嚴(yán)格執(zhí)行經(jīng)營(yíng)目標(biāo)責(zé)任制度,每月定期召開(kāi)生產(chǎn)質(zhì)量例會(huì),利用PPT圖文并茂的形勢(shì)進(jìn)行分解。大力倡導(dǎo)無(wú)紙自動(dòng)化辦公,上傳日?qǐng)?bào)表到局域網(wǎng),開(kāi)放每月22號(hào)的總經(jīng)理接待日,讓員工參與到企業(yè)的民主管理,從而有效降低生產(chǎn)和管理成本,實(shí)現(xiàn)了經(jīng)濟(jì)效益最大化。
在生產(chǎn)技術(shù)上,該公司努力創(chuàng)新,成功改變傳統(tǒng)濕紗含油檢測(cè)方法,每月節(jié)約用油15噸左右,同時(shí)含油合格率也得到了有效控制;成型車(chē)間率先實(shí)行分通路對(duì)質(zhì)量進(jìn)行考核的獎(jiǎng)懲制度,使成型生產(chǎn)班的每一個(gè)管理人員都擁有自己?jiǎn)为?dú)的考核體系,大大提高了原絲質(zhì)量;“555”量產(chǎn)的有效實(shí)施,為創(chuàng)新項(xiàng)目從理論到實(shí)現(xiàn)提供了有力保證;推行“5S”現(xiàn)場(chǎng)管理,使得各生產(chǎn)工序作業(yè)環(huán)境井然有序。
同時(shí),該公司將電助熔和均化庫(kù)成功投入使用,從而使得玻璃液變得更優(yōu)質(zhì),生產(chǎn)作業(yè)更加穩(wěn)定并且減少了廢氣量的排放;減少粉料流失,作業(yè)環(huán)境得到明顯改善;二通路全面安裝完成雙流體噴霧,使其涂覆率能達(dá)到85%,可燃物含量值提升0.05%-0.1%;提重工作的順利完成使得成品率大幅提高,有效降低了生產(chǎn)成本;成立浸潤(rùn)劑油耗攻關(guān)小組,并有針對(duì)性地進(jìn)行整改,使得耗達(dá)到了歷史最好水平。
此外,該公司還通過(guò)分別對(duì)拉絲機(jī)工藝、機(jī)械手及板鏈安裝位置、高腳排線(xiàn)重新設(shè)計(jì)、分束板代替分束輪、漏板作業(yè)進(jìn)行改進(jìn)等方式,解決了短切紗及透明板材紗的脫圈問(wèn)題,提高了直接紗外觀和內(nèi)在質(zhì)量,分束紗存在的“脫圈”、“并條”問(wèn)題也得以妥善解決。