上世紀(jì)九十年代,汽車制造商開始使用注塑成型工藝,以短切玻纖增強(qiáng)熱塑性復(fù)合材料替代金屬,來(lái)生產(chǎn)油門踏板。
而制動(dòng)踏板,也就是人們俗稱的“腳剎”,卻因?yàn)榕c汽車的安全性有著更為密切的關(guān)系,對(duì)自身的強(qiáng)度、剛度、扭轉(zhuǎn)載荷有著更高的要求,彼時(shí)尚未實(shí)現(xiàn)從金屬向復(fù)合材料的轉(zhuǎn)變。
來(lái)自德國(guó)的汽車一級(jí)供應(yīng)商Boge Rubber & Plastics Group(以下簡(jiǎn)稱Boge)宣稱推出了世界上首個(gè)量產(chǎn)熱塑性復(fù)合材料汽車制動(dòng)踏板,滿足了汽車廠對(duì)安全性和經(jīng)濟(jì)性的要求。
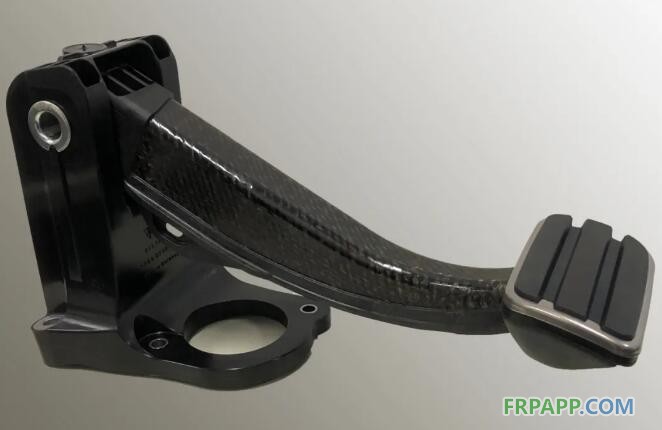
這款創(chuàng)新的制動(dòng)踏板采用了獨(dú)特的設(shè)計(jì)方案,混合使用了三種不同的復(fù)合材料,引入了與眾不同的生產(chǎn)工藝。
Boge公司專業(yè)從事汽車減振、傳動(dòng)、底盤、輕量化模塊以及踏板箱(包括制動(dòng)、離合、油門)相關(guān)零部件的研發(fā)和生產(chǎn)。自2008年起,公司開始使用連續(xù)纖維有機(jī)板和短切玻纖,利用復(fù)合模塑工藝(overmoulding)生產(chǎn)汽車零部件。2018年,又引入了熱塑性單向帶,并通過(guò)工藝的創(chuàng)新縮短了生產(chǎn)周期、降低了成本、擴(kuò)大了業(yè)務(wù)量。
“2015年的某一天,老板跟我說(shuō),這些創(chuàng)新都很不錯(cuò),但是如果能尋找到更大的應(yīng)用市場(chǎng),把用量提升上去就更好了。”Boge公司全球創(chuàng)新中心總經(jīng)理Daniel Häffelin博士工程師表示,“于是,我們的工程師團(tuán)隊(duì)一起做了頭腦風(fēng)暴,最后把目光聚焦到汽車制動(dòng)踏板這一細(xì)分產(chǎn)品上了。”
想要說(shuō)服汽車制造商采用新的產(chǎn)品,必須充分證明它的經(jīng)濟(jì)性。“我們認(rèn)為現(xiàn)有工藝已經(jīng)把生產(chǎn)周期壓得夠短了,進(jìn)一步下調(diào)的空間有限,所以唯一的出路就是通過(guò)提高纖維的使用效率來(lái)降低成本。”
然而,簡(jiǎn)單地減少用量,把制動(dòng)踏板做得更小、更薄顯然行不通,因?yàn)橹苿?dòng)踏板對(duì)形狀和尺寸有嚴(yán)格的要求,更不用說(shuō)對(duì)它關(guān)系著汽車的整體安全性能。因此,研究的方向鎖定在如何對(duì)纖維取向進(jìn)行精準(zhǔn)的控制,從而減少部件的壁厚和非關(guān)鍵區(qū)域的纖維用量上。
“想要減少纖維用量,還要保持足夠的強(qiáng)度和剛度,在運(yùn)動(dòng)和醫(yī)療市場(chǎng)上的通常做法是引入拾-放設(shè)備(Pick-and-Place),但是那樣做太貴了。”Boge公司首席執(zhí)行官Torsten Bremer博士表示,“于是,我們不得不嘗試尋找新的工藝路徑。”
“當(dāng)時(shí)我們已經(jīng)開始和一些汽車廠家合作研發(fā)全復(fù)合材料制動(dòng)踏板。”Boge公司執(zhí)行副總裁Burkhard Tiemann回憶說(shuō),“我們?cè)?015年向他們做出了承諾,3年后我們做出了第一批產(chǎn)品。”
三種材料的混合使用
Boge公司針對(duì)制動(dòng)踏板的不同位置分別使用了三種不同的材料。
1. 殼結(jié)構(gòu)是踏板的主要承重結(jié)構(gòu),需耐受最高3000牛頓的壓力,同時(shí)還需要保證它足夠輕薄、性價(jià)比足夠高。為此,Boge公司選用了德國(guó)朗盛公司生產(chǎn)的連續(xù)玻纖有機(jī)板。
2. 對(duì)于有機(jī)板上需要局部增強(qiáng)的部分,Boge公司使用了美國(guó)塞拉尼斯公司提供的單向玻纖帶,并遵照汽車廠商對(duì)特定溫濕度條件下材料應(yīng)變曲線的要求,通過(guò)有限元分析的方法計(jì)算出鋪放的路徑。
3. 另外,為實(shí)現(xiàn)踏板中的功能性幾何形狀,Boge公司使用了由多個(gè)供應(yīng)商提供的短切玻纖,利用復(fù)合模塑工藝形成加強(qiáng)筋和其他輔助結(jié)構(gòu)。
與上述3種增強(qiáng)材料配合使用的基體材料,是已在汽車行業(yè)中廣泛采用的黑色尼龍6。如果汽車廠商另有要求,Boge公司亦可在復(fù)合模塑工藝過(guò)程中使用尼龍6,6作為替代。
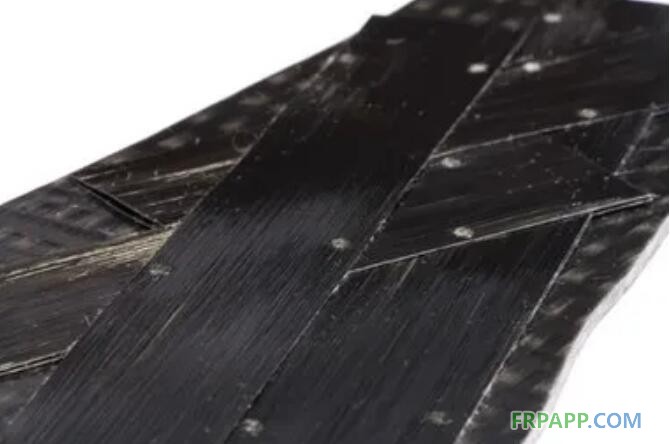
通過(guò)混合使用三種不同形態(tài)的玻纖增強(qiáng)材料,Boge公司實(shí)現(xiàn)了對(duì)纖維取向的精確控制,既滿足了制動(dòng)踏板的性能要求,又避免了材料的浪費(fèi)、減少了壁厚、縮短了生產(chǎn)周期、降低了部件成本。
工藝流程
通過(guò)與德國(guó)自動(dòng)化生產(chǎn)線制造商M.A.i. GmbH & Co. KG的合作,Boge公司為這款全熱塑性復(fù)合材料制動(dòng)踏板設(shè)計(jì)了一套三步走的工藝路線,實(shí)現(xiàn)了1)1分鐘快速成型;2)高度自動(dòng)化;3)個(gè)性訂制化。
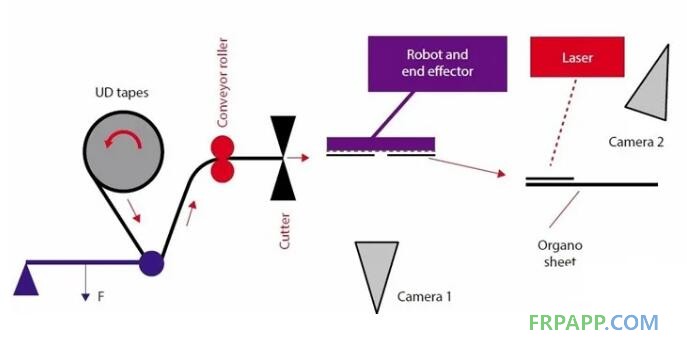
生產(chǎn)開始前,工作車間里先備好兩堆經(jīng)過(guò)預(yù)成型的有機(jī)板和四卷單向玻纖帶。
1. 生產(chǎn)開始時(shí),機(jī)器人拾取一片有機(jī)板,將其移至工作臺(tái)上;同時(shí),將單向玻纖帶裁至所需長(zhǎng)度,置于傳送帶之上。接著,輪轉(zhuǎn)式拾放設(shè)備(Pick-and-Place)依次拾取四條單向帶,在此過(guò)程中由監(jiān)控?cái)z像頭檢查每條單向帶的質(zhì)量、尺寸和位置是否符合要求。然后,設(shè)備按照程序中寫入的位置依次將單向帶貼到有機(jī)板表面,并用激光進(jìn)行多點(diǎn)焊接,防止單向帶發(fā)生位移。
此過(guò)程不間斷,直至設(shè)計(jì)方案中所有單向帶全部貼至有機(jī)板上的正確位置。整個(gè)過(guò)程完全通過(guò)數(shù)控技術(shù)實(shí)現(xiàn),客戶的個(gè)性化需求可以通過(guò)調(diào)整程序充分滿足。所有環(huán)節(jié)都在攝像頭及傳感器的監(jiān)控下完成,確保生產(chǎn)過(guò)程與設(shè)計(jì)方案完全一致。
2. 而后,為保證生產(chǎn)效率,經(jīng)過(guò)局部增強(qiáng)的有機(jī)板被送入紅外加熱爐進(jìn)行預(yù)加熱。在此過(guò)程中,單向帶和有機(jī)板中的特殊抗氧化成分會(huì)保護(hù)樹脂系統(tǒng)免于熱損傷。進(jìn)而,完成預(yù)熱的有機(jī)板被快速送入預(yù)成型腔,在高壓條件下彎折成U型,并保證較高的表面質(zhì)量。同樣地,這個(gè)過(guò)程也全程受到質(zhì)量監(jiān)控。
3. 最后,溫?zé)岬念A(yù)制件被轉(zhuǎn)入注塑模具,與短切玻纖增強(qiáng)尼龍復(fù)合材料進(jìn)行復(fù)合模塑,生成包括加強(qiáng)筋在內(nèi)的輔助幾何結(jié)構(gòu)。完成脫模后,進(jìn)行快速的修剪和檢查,但無(wú)需噴漆或表面處理。
未來(lái)市場(chǎng)
該全熱塑性復(fù)合材料制動(dòng)踏板,尺寸為350 × 90 × 60毫米。與早先的設(shè)計(jì)方案相比,有機(jī)板用量減少了33%,名義壁厚從3毫米降至2毫米。
它的重量約為金屬踏板的一半,強(qiáng)度與后者相近,甚至高于后者,有助于提升駕駛者的駕駛體驗(yàn);它的生產(chǎn)成本與鋁制踏板近似、略高于鋼制踏板。
另外,每個(gè)踏板都擁有自己的專屬身份二維碼,便于日后溯源。
2018年,這款全熱塑性復(fù)合材料汽車制動(dòng)踏板進(jìn)入量產(chǎn)階段,單個(gè)部件的生產(chǎn)周期約為1分鐘,現(xiàn)有生產(chǎn)線的年產(chǎn)量可達(dá)到100萬(wàn)件。
“隨著汽車行業(yè)逐漸向電動(dòng)方向發(fā)展,制動(dòng)踏板的設(shè)計(jì)也將因?yàn)殡姎饣傻囊笞兊酶訌?fù)雜,這將賦予復(fù)合材料更大的競(jìng)爭(zhēng)力。” Häffelin博士表示。