層壓工藝是層壓成型中的重要工序。層壓工藝是將浸漬膠布按壓制厚度要求配迭成板坯,置于兩個(gè)拋光的金屬模板之中,放在熱壓機(jī)上,對(duì)兩層模板之間加熱、加壓,經(jīng)熱壓固化后冷卻脫模。
一、層壓設(shè)備
主要設(shè)備為熱壓機(jī)組。輔助設(shè)備有裝卸機(jī)、模板回轉(zhuǎn)機(jī)、模板清洗機(jī)、鋪模清理機(jī)(疊鋪機(jī))等設(shè)備。從生產(chǎn)組合上分單機(jī)熱壓、冷卻和兩臺(tái)熱壓、冷卻機(jī)。
目前國(guó)內(nèi)外使用的熱壓機(jī)有2種:開式壓制熱壓機(jī)和封閉真空熱壓機(jī)。與開式熱壓機(jī)相比,真空熱壓機(jī)具有兩個(gè)突出優(yōu)點(diǎn):①成型單位壓力低1/2-1/3,即降低膠的流動(dòng),布的經(jīng)緯線移動(dòng)小,降低層壓板的內(nèi)應(yīng)力,最終達(dá)到降低翹曲度的目的;②可避免板內(nèi)和邊角產(chǎn)生氣泡,產(chǎn)品的質(zhì)量較高;真空熱壓在復(fù)合材料成型中的應(yīng)用越來越廣泛。
熱壓機(jī)的性能和控制水平直接影響產(chǎn)品的質(zhì)量,同時(shí)與成型工藝有直接關(guān)系。熱壓機(jī)主要控制加熱板的溫度場(chǎng)和壓力。
1.加熱板
加熱板的結(jié)構(gòu)和所使用的熱介質(zhì)直接影響加熱板的溫度場(chǎng)的均勻性、板面溫度的均勻性、膠布膠熔化的均勻性,以及膠化后產(chǎn)生的氣體和膠布層間的空氣的排出。因此加熱板升溫速度要快且均勻,板面溫度差應(yīng)小于3℃。
加熱板的通道有單進(jìn)單出和雙進(jìn)雙出兩種。后者制造復(fù)雜,配管也復(fù)雜,成本高,一般很少采用。前者采用蒸汽加熱,板面溫度差較大(大約5℃);當(dāng)采用熱水或?qū)嵊蜁r(shí),板面溫度差低于3℃;采用導(dǎo)熱油效果更好,因?yàn)閷?dǎo)熱油的壓力低(小于0.5MPa)、溫度高(可達(dá)300℃左右)。
對(duì)整機(jī)溫度控制,一般熱壓機(jī)開口12-20個(gè),這樣加熱板從下而上呈現(xiàn)溫度梯度。蒸汽加熱為單點(diǎn)總控較多,梯度大約5℃左右。熱水或?qū)嵊鸵话悴捎梅謪^(qū)(一般分2-3個(gè)區(qū))控制,溫度梯度只是控制誤差低于3℃,這樣有利于在同一壓力下,上、中、下的固化速度相同,有利于提高產(chǎn)品質(zhì)量。
2.壓力
目前熱壓大都采用液壓機(jī),可滿足產(chǎn)品成型所需的單位壓力,最高可達(dá)12.5MPa,壓力穩(wěn)定小于±500KPa,可根據(jù)工藝要求設(shè)定。多層壓機(jī)的噸位一般較大,通常為2000-3000t。圖5-6為2800噸多層壓機(jī)實(shí)物圖。

二、層壓工藝過程
1.膠布裁剪、配迭
膠布裁剪是將膠布剪成一定尺寸(按壓機(jī)大小),剪切設(shè)備可用連續(xù)定長(zhǎng)切片機(jī),也可以手工裁剪。膠布的剪切要求尺寸準(zhǔn)確,不能過長(zhǎng)或過短。將剪好的膠布整齊疊放,把不同含膠量及流動(dòng)性的膠布分別堆放,做好記號(hào)儲(chǔ)存?zhèn)溆?。為了盡可能地避免膠布揮發(fā)份的增加及可溶性樹脂含量的降低,膠布應(yīng)貯存在干燥室內(nèi)。
不同用途浸膠布的裁剪方式也不同:用于層壓的膠布按生產(chǎn)規(guī)格進(jìn)行裁剪,同時(shí)留有加工毛邊的余量;用于布帶纏繞的膠布則先把膠布切割成纏繞成型所要求的膠布帶,然后通過縫紉搭接、倒盤、卷成一定直徑的膠布帶盤使用。
膠布配迭工序?qū)訅喊宓馁|(zhì)量好壞至關(guān)重要,如配迭不當(dāng)會(huì)發(fā)生層壓板裂開、表面花麻等弊病。所以在具體操作中應(yīng)注意如下幾點(diǎn):
1)在配迭板材的面層,每面應(yīng)放2~3張表面膠布,其含膠量和流動(dòng)性應(yīng)比里布略高。
2)揮發(fā)物含量不宜太大。如果揮發(fā)物含量太大,應(yīng)干燥處理后再用;否則會(huì)影響制品的電性能、耐熱性,易產(chǎn)生邊角氣泡及花麻。
3)配迭的計(jì)算。要使壓制的板材厚度準(zhǔn)確,一般采用質(zhì)量法確定板材的膠布用量。每塊板材所需膠布(或膠紙)材料的質(zhì)量與層壓板的厚度、面積、成板后的密度及成板后切去廢邊率的因素有關(guān)。
計(jì)算公式p=Fhd×(1+a)/1000
式中p—需要層壓膠布(紙)的總質(zhì)量,g;
F—壓制板材的面積,cm2;
h—壓制板材的厚度,cm;
d—成品板的密度,g/ cm3;
a—修正系數(shù)。
密度在壓制布質(zhì)、紙質(zhì)板時(shí)按1.40~1.45;環(huán)氧酚醛玻璃布板按1.65~1.70計(jì)算(視含膠量和浸漬材料的坯重而定)。α的大小視成品板厚度而定,h<5mm時(shí),α取0.02~0.03,h>5mm時(shí),α取0.03~0.08。
大面積的層壓板可先取幾張膠布(紙),稱取質(zhì)量,確定1mm所需膠布(紙)的厚度,然后視要求厚度點(diǎn)清張數(shù)。
2.熱壓工藝
將裝料車的組合推入多層壓機(jī)的熱板中間,熱板緩緩上升,閉合后加壓通入蒸汽壓制。
壓制工藝中的關(guān)鍵是確定工藝參數(shù),其中最重要的參數(shù)是溫度、壓力和時(shí)間。壓力制度首先取決于物料的品種和性質(zhì),其次考慮制品的厚度、板面積和設(shè)備條件。
1)溫度
一般壓制工藝的升溫過程可分為5個(gè)階段,如圖5-7所示。
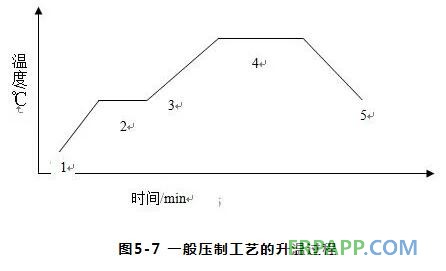
第一階段是從室溫升到物料顯著反應(yīng)溫度,即預(yù)熱階段。此時(shí)樹脂熔化并排出部分揮發(fā)物,壓力一般為全壓力的1/3~1/2。
第二階段是中間保溫階段。這時(shí)樹脂熔化、滲透,反應(yīng)速度較低。保溫時(shí)間根據(jù)膠布老嫩程度和制品板的厚度而定。當(dāng)流出樹脂接近凝膠化并拉長(zhǎng)絲時(shí),應(yīng)加大壓力并升溫。
第三階段為升溫階段。這是為了提高樹脂固化程度。此時(shí),樹脂反應(yīng)速度加快。
第四階段為保溫階段,目的是使樹脂充分固化,該溫度取決于樹脂的固化特性,而固化時(shí)間則取決于板材的厚度。
最后階段為冷卻階段,達(dá)到保溫階段終點(diǎn)即可停止加熱,然后緩慢冷卻,并保持所需的最高壓力。冷卻速度對(duì)制品表面的平整度有影響,應(yīng)控制冷卻速度,開始冷卻時(shí)不宜過快,降至50℃以下時(shí)才脫模。
2)壓力
壓力的作用是用來克服揮發(fā)物的蒸汽壓,使粘結(jié)樹脂流動(dòng),使膠布層間密切接觸,防止板材冷卻時(shí)變形。
成型壓力的大小根據(jù)根據(jù)樹脂的固化特性確定。固化時(shí)若有小分子物逸出,壓力應(yīng)大一些;樹脂固化溫度高時(shí),成型壓力也要相應(yīng)增大。成型壓力的大小還需考慮制品的厚度、膠布的含膠量和升溫速率等因素。
幾種常見的玻璃布層壓板的工藝參數(shù)見表5-7。
表5-7 幾種層壓板材的熱壓制度
3)時(shí)間
從預(yù)熱加壓開始到取出制品為止的時(shí)間即壓制時(shí)間,它是預(yù)壓、熱壓和冷卻時(shí)間之和,壓制時(shí)間與樹脂的固化速度,層壓板的厚度和壓制溫度有關(guān),以層壓板能否被充分固化為依據(jù)。
預(yù)壓時(shí)間取決于膠布的性能,若膠布的不溶性樹脂含量高,揮發(fā)份含量低,則預(yù)壓時(shí)間就短,反之要相對(duì)延長(zhǎng)。熱壓時(shí)間以保證膠布中樹脂充分固化,太短則樹脂固化不完全,太長(zhǎng)則是制品性能下降,需要通過反復(fù)試驗(yàn)來確定。冷卻時(shí)間是保證產(chǎn)品質(zhì)量的最后一個(gè)環(huán)節(jié),冷卻時(shí)間過短則容易使產(chǎn)品產(chǎn)生翹曲、開裂等現(xiàn)象;太長(zhǎng)則降低生產(chǎn)效率。
3.冷卻脫模
保溫結(jié)束后即可關(guān)閉熱源,自然降溫或采用冷風(fēng)、冷水等冷卻,但不應(yīng)過早降壓,否則會(huì)使產(chǎn)品表面起泡或產(chǎn)生翹曲現(xiàn)象。脫模溫度一般低于60℃。
4.后處理
后處理的目的是使樹脂進(jìn)一步固化直到完全固化,同時(shí)部分消除制品內(nèi)的應(yīng)力,提高制品的性能。環(huán)氧板、環(huán)氧酚醛板的后處理是在120~130℃溫度的環(huán)境中持續(xù)120~150分鐘,這樣可提高制品的機(jī)械性能和電氣性能。
三、層壓板性能
幾種典型層壓板產(chǎn)品的部分性能見表5-8。
表5-8 幾種典型層壓板產(chǎn)品的部分性能
四、制品缺陷的分析及對(duì)策
以膠布為原料的層壓板在生產(chǎn)中可能出現(xiàn)如下主要質(zhì)量問題見表5-9。
表5-9 層壓板常見質(zhì)量問題及解決措施
實(shí)際生產(chǎn)時(shí)出現(xiàn)的問題還遠(yuǎn)不止這些,應(yīng)針對(duì)不同問題具體分析,作出正確判斷,不斷總結(jié),問題是可以解決的。