先進樹脂基復(fù)合材料具有優(yōu)異的性能,應(yīng)用前景廣闊,但是由于目前較多地采用熱壓罐成型工藝制備,存在成本較高、制件尺寸受限制等因素,因此復(fù)合材料工作者不斷研究各種非熱壓罐成型工藝,其中真空袋成型工藝由于具有靈活、簡便、高效等特點得到廣泛的應(yīng)用。
真空袋成型工藝的主要設(shè)備是烘箱或其他能提供熱源的加熱空間, 其組裝方法一般與熱壓罐工藝類似。對于熱壓罐成型工藝,由于工藝過程中施加較高的壓力(通常為0. 3~0. 7MPa) ,大部分材料中的孔隙通過真空系統(tǒng)逸出或隨著多余樹脂的流出而排出,剩余的孔隙發(fā)生壓縮、破碎并溶解在基體中,從而得到低孔隙含量的復(fù)合材料,特別是不會遺留下大尺寸的缺陷。但是在真空袋成型工藝中,由于真空壓力最多為一個大氣壓,孔隙和揮發(fā)分只能通過逸出的方式排出,因此與熱壓罐成型工藝相比,預(yù)浸料鋪層中的孔隙和揮發(fā)分的處理是一個問題,所制備材料的孔隙率通常為3%或更高, 而高孔隙含量會直接影響到復(fù)合材料的力學性能和耐濕熱性能。
針對這一問題,主要存在兩種技術(shù)路徑,一種是從樹脂體系入手,調(diào)節(jié)樹脂的流變特性,使孔隙和揮發(fā)分在預(yù)浸料凝膠前盡可能逸出;另一種途徑就是通過工藝措施的改進,使預(yù)浸料中的孔隙和揮發(fā)分在制備過程中更容易排出,雙真空袋(DB)成型工藝就是這種途徑的有益嘗試。
從上世紀80年代開始,美國Naval Air Warfare Center和NASA Langley Research Center就相繼開展了多種樹脂體系和多種形式的雙真空袋成型工藝的研究[ 1~4 ] ,雙真空袋成型工藝就是在預(yù)浸料毛坯上封兩層真空袋,兩層真空袋之間放置一導(dǎo)氣工裝,兩層均與真空系統(tǒng)連接,其原理就是在復(fù)合材料固化過程中,在預(yù)浸料處于B階段時,使預(yù)浸料鋪層暴露在真空中但同時并不承受任何壓實的作用力,從而促使預(yù)浸料毛坯中的孔隙和樹脂中的揮發(fā)分能夠很容易地逸出。本工作將通過對雙真空成型工藝的研究,對通常的真空袋成型工藝進行改進,以提高真空袋成型工藝制備的復(fù)合材料的品質(zhì)。
1、試 驗
采用LT203 /T700SC復(fù)合材料體系,推薦工藝為:在室溫抽真空,以每分鐘2~3℃的速率升溫至75℃,恒溫7h,然后以不大于0. 5℃ /m in的速度冷卻至40℃以下取出制件。
由于雙真空袋工藝只是在一定階段采用雙真空的模式,該階段的設(shè)置需要結(jié)合具體樹脂體系的流變特性和凝膠特性來研究確定。LT203樹脂體系的粘度- 溫度曲線(升溫速率為2℃ /min) 如圖1所示,樹脂在30℃時具有較高的粘度,開始升溫后粘度迅速下降,在約55℃時降至10Pa.s,然后一直到約90℃以前均處于一個低粘度區(qū)間。試驗過程中分別在高粘度區(qū)和低粘度區(qū)進行工藝設(shè)置如圖2所示,分別在30℃, 55℃, 65℃和75℃設(shè)置雙真空工藝平臺,以考察工藝對樹脂粘度的依賴性。同時進行真空袋工藝的對比試驗,然后根據(jù)分析測試結(jié)果來對工藝進行評價和優(yōu)化。
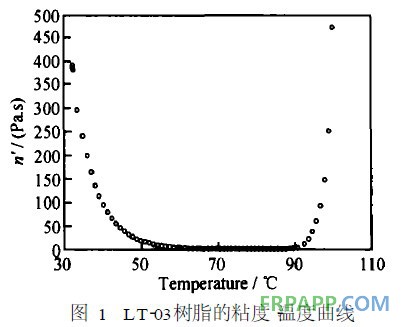
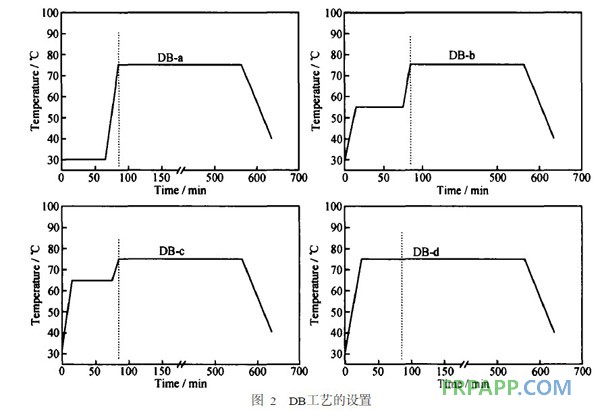
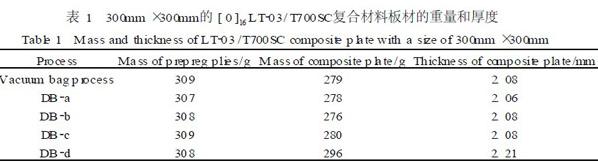