1 引言
發(fā)展更高效率熱機的關(guān)鍵在于提高工作溫度,而提高工作溫度之關(guān)鍵又取決于更高工作溫度材料的研制。鎳、鈷基高溫合金已發(fā)展到接近其使用溫度的極限,因此要進一步提高發(fā)動機的效率,就必須研制和發(fā)展陶瓷基復合材料。連續(xù)纖維增強陶瓷基復合材料(CFCC)是最有希望滿足發(fā)動機高溫部件要求的材料,而制造CFCC的工藝則是其中最關(guān)鍵的問題。傳統(tǒng)的熱壓燒結(jié)工藝會大大損傷纖維,并使纖維和基體發(fā)生嚴重的化學反應[1~3]。溶膠-凝膠法(sol-gel)和化學氣相沉積(CVD)或滲透(CVI)則是制造CFCC的較好方法,但使用溶膠-凝膠法生產(chǎn)出的復合材料密度較低,制造溫度仍較高(約1300~1400℃),而且還需加壓,不夠理想。而CVD(CVI)只能沉積簡單的薄壁件,如單層纖維薄片或薄殼型材料。對于粗厚型件內(nèi)部往往出現(xiàn)孔洞,存在著致密性差(一般只能達到理想密度的70%~80%)[4]、不易成型且沉積時間過長等問題。為了解決上述問題我們提出了一種新工藝新方法PCCVD即位控化學氣相沉積法,并進行了初步試驗。
2 實驗方法
2.1 實驗材料
通過PCCVD來制造碳纖維增強碳化硅復合材料。本工藝選用高模量碳纖維(抗張強度為2.2GPa,抗張模量為360GPa,密度為1.8g/cm3)和甲基三氯硅烷(MTS)。MTS的純度約為94%。使碳化硅基體沉積在碳纖維預制件上。
2.2 PCCVD的原理
在傳統(tǒng)的CVD工藝中,反應氣體是通過載氣(或許參加也可能不參加反應)攜帶到加熱的預制件上,在預制件的表面,氣體反應形成固體沉積物,而反應生成的氣體由載氣帶出沉積系統(tǒng)。在沉積過程中,整個預制件里外同時沉積,由于預制件的外部比內(nèi)部有更多的機會接觸反應氣體,而迅速達到完全沉積。結(jié)果,通向預制件內(nèi)部的入口被封閉[5],使得反應物從反應氣體到預制件內(nèi)部纖維表面的物質(zhì)交換和生成物從纖維表面到主氣流的物質(zhì)交換變得非常困難。最后,從復合材料的表面上看,得到了完全的沉積,但其內(nèi)部存有較多的氣孔。另一方面,由于復合材料的表面是不受限制的沉積,所以復合材料的外形達不到所規(guī)定的尺寸要求。
PCCVD通過控制試樣的加熱位置,控制反應氣體通道位置,從而達到控制沉積位置的三位控沉積法。PCCVD不是在整個試樣上同時沉積,而是在一個不斷移動的截面上沉積,此截面是試樣中已沉積的部分與未沉積部分的交界面,稱為沉積界面。當沉積界面從試樣的一端移到另一端時,整個試樣就沉積好了。在沉積過程中,試樣中未沉積部分的內(nèi)部孔隙一直是與外部相通的,反應氣體始終可以在沉積界面上充分流動,全部是開口沉積。這樣沉積出來的密度是比較高的,試驗中最高可達其理論密度的96%。圖1為PCCVD的工藝簡圖。
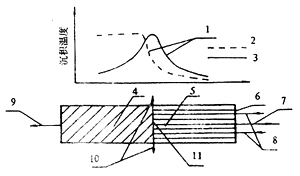
圖 1 PCCVD的工藝簡圖
1模子中的溫度分布;2溫度分布;3溫度峰;4完全沉
積部分;5未沉積部分;6模子和預制件;7沉積界面的移動方向;
8氣體試劑的流動方向;9模子的移動方向;10沉積界面上主氣
流的流動方向;11沉積界面
PCCVD技術(shù)很復雜,由于整個過程中發(fā)生著物理和化學變化及相互作用,使用PCCVD制造的復合材料其性能受很多因素的影響,如:碳纖維的類型、模子和預制件的設計及MTS的純度等,但最重要的先決條件包括:
(1) 靠近沉積界面有一陡的溫度梯度并且該溫度峰值等于沉積溫度;
(2) 沉積界面上溫度梯度的方向基本與主氣流的流動方向垂直。在放試樣的模具內(nèi)部與外部應產(chǎn)生一定的壓力差,迫使反應氣流經(jīng)沉積界面后流出;
(3) 沉積界面以一定的速度在沿溫度梯度方向移動并且移動速度必須與預制件中碳化硅的沉積速度相匹配;
(4) 將反應氣體引入模子通過沉積界面,迫使其在沉積界面上進行反應,然后由泵將反應后的氣體從模子中抽出。
2.3 模具
模具的設計是PCCVD中重要的一環(huán)。本實驗采用石墨模具。使用這種模具可使反應氣體全部流經(jīng)試樣,而且是從沉積界面流出,從而使大部分硅烷得到利用。該模具還具有易于加工、容易脫模等優(yōu)點。
2.4 PCCVD的反應室
PCCVD的反應室示于圖2。反應室由石英制成,其中部有一個具有特定幾何形狀并能在長度方向產(chǎn)生溫度梯度(參見圖1)的石墨感應發(fā)熱體。最初將裝有碳纖維的模子置于石墨感應發(fā)熱體的下端,當將模子以適當?shù)乃俣纫七M感應發(fā)熱體里時,其移進石墨感應體里的部分通過輻射加熱形成一個達到沉積溫度的熱區(qū)。MTS和載氣通過一根管子被直接插進模子內(nèi)部。反應室里為負壓。由于模子與管子間的密封,把氣體送入相對于反應室為正壓的預制件內(nèi)部,這樣模子內(nèi)部與外部間會產(chǎn)生一個壓力差,迫使氣體流過碳纖維預制件。移進沉積溫度區(qū)的碳纖維預制件部分開始沉積,而未移進該區(qū)的部分仍有氣體流過,沉積界面上的沉積隨模子逐漸移進感應發(fā)熱體逐步地進行,一旦基體達到完全沉積時流過模子的氣體將被阻止。
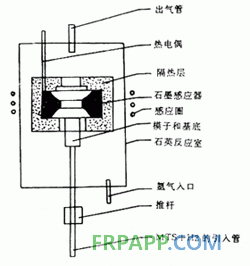
圖 2 PCCVD反應室的簡圖
3 實驗結(jié)果與討論
PCCVD是制造纖維增強陶瓷特別是連續(xù)纖維增強陶瓷復合材料的新方法。通過改變PCCVD的工藝參數(shù)來研究其對沉積的影響程度,以便控制沉積條件。
本實驗用于沉積的標準條件為:沉積溫度1150~1250℃,氣流速度為60cm3/min,氫氣與MTS之比為10∶1,模子移動速度(也可以說是沉積界面移動速度)為0.5mm/min。碳纖維預制件的尺寸為3mm×4mm×50mm。纖維的體積含量約為50vol%。由PCCVD制造的C/SiC復合材料SEM分析結(jié)果示于圖3a和圖3b。
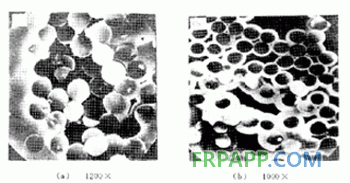
圖 3 用PCCVD制造的C/SiC的SEM像
由圖3a可見,所有的碳纖維幾乎都被SiC基體所包圍,其中幾乎不含氣孔。由圖3b可以看出,由于模子的移動速度較高,仍存在著一些氣孔。
按上述條件制備的C/SiC復合材料,當模子移動速度為2.5mm/30min、纖維體積含量為50vol%時,其密度已達到2.44g/cm3,試樣密度為理論密度的96%。
PCCVD能沉積出比較致密的試樣的關(guān)鍵所在是必須使沉積界面上有新鮮的反應氣體流過。如果模子移動速度過慢,該工藝反應時間將很長,而其速度過快,碳化硅基體中將有很多氣孔。氣孔的形成與模子移速度之間的關(guān)系如圖4所示。其中圖4a,由于模具的推進速度和SiC的沉積速度相匹配,因此沉積界面比較平坦。而圖4b則因推進速度較快,在沉積界面上還未沉積好,高溫區(qū)已推向前進,致使已有的沉積界面未沉積好,又形成新的沉積界面,從而形成一個開口的瓶狀的未沉積區(qū)。這時,反應氣體難以進入“瓶”內(nèi),而“瓶”口由于接觸新鮮的反應氣體較多沉積速度快,最終如圖4c所示,把“瓶”口封死,形成孔隙。因此,PCCVD的關(guān)鍵是在沉積溫度下,硅烷氣體供應充足時,模具的推進速度必須等于或小于SiC沉積速度。這時,存在一個最大移動速度。影響復合材料密度的主要參數(shù)為模子的移動速度和纖維體積分數(shù),一般說纖維的體積分數(shù)愈大允許的模子移動速度愈快。
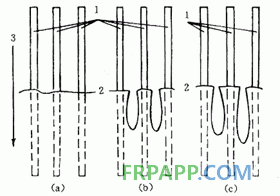
圖 4 氣孔的形成簡圖
1碳纖維;2沉積界面;3模子的移動方向。
在標準條件下,模子的移動速度V對復合材料的密度D的影響如圖5所示。D與V基本滿足下邊的表達式:
D/DT=(1-V1.8)1/2
其中DT為理論密度。
由圖5可知,模子的最大允許移動速度約為0.3mm/min,這時其實際密度可達其理論密度的96%左右。對于3mm×4mm×50mm的試樣需要160min達到完全沉積。
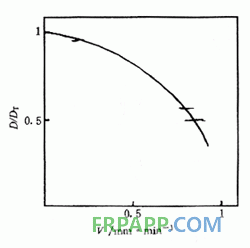
圖 5 標準條件下模子的移動速度對復合材料的密度的影響
4 結(jié)論
PCCVD是制造纖維增強陶瓷基復合材料并對纖維無損傷且不產(chǎn)生氣孔的新方法。由PCCVD制造的C/SiC CFCC,當纖維的體積分數(shù)約為50vol%時,其密度已達到2.44g/cm3,為理論密度的96%。