0·前言
環(huán)氧樹脂(EP)膠粘劑具有優(yōu)異的力學(xué)性能和粘接性能,并且其價格較低、成型工藝簡單[1-2]。EP室溫固化是節(jié)能型固化方式,在大型結(jié)構(gòu)件中具有獨 特優(yōu)勢(如不便加熱的大型結(jié)構(gòu)件的制造[3]、自然條件固化的低廉成本和優(yōu)異的力學(xué)性能等),也是廣泛應(yīng)用于國民經(jīng)濟和軍事等各領(lǐng)域中的主要原因。傳統(tǒng)EP室溫固化體系的不足之處:① 脂肪族多胺固化劑(如乙二胺、二乙烯三胺等)體系的凝膠時間過短、操作不便(有的為固體,使用時需加熱)、韌性較差且配比要求太嚴 ;② 咪唑類固化劑體系的固化時間過長,其室溫適用期為0.5~7 d;③ 叔胺類固化劑(如DMP一30)體系的室溫凝膠時間為70 min左右,難以滿足大型結(jié)構(gòu)件所需的操作期。
本研究以兼具固化劑、引發(fā)劑和稀釋劑等功能的自制BH一1為固化劑,同時引入低黏度活性稀釋劑(芐基縮水甘油醚),有望制備出一種凝膠時間約為8.5 h、配比要求不嚴、在較寬溫度范圍內(nèi)均可獲得滿意熱力學(xué)性能的EP室溫(25 ℃)固化膠粘劑。
1·試驗部分
1.1 試驗原料
環(huán)氧樹脂(EP),工業(yè)級(牌號E一5l,環(huán)氧值0.51),大連齊化化工有限公司;叔胺類固化劑(BH一1),自制;丙酮,化學(xué)純,西安化學(xué)試劑總廠;芐基縮水甘油醚(活性稀釋劑),化學(xué)純(25℃黏度5~10 mPa·S),常熟佳發(fā)化學(xué)有限責(zé)任公司。
S一玻璃纖維簾子布,南京玻璃研究設(shè)計院。
1.2 試驗儀器
CS101一lAB型電熱干燥箱,重慶銀河實驗儀器有限公司;CMT型萬能試驗機、ZBC一4型沖擊試驗機、83001 1型拉力試驗機,深圳新三思材料檢測有限公司;NDJ一79型旋轉(zhuǎn)黏度計,上海昌吉地質(zhì)儀器有限公司;2910型差示掃描量熱分析儀,美國TA公司。
1.3 試驗制備
1.3.1 EP澆鑄體的制備
將EP在80℃時抽真空脫泡若干時間,然后加入BH一1,攪拌均勻;隨后將上述物料澆鑄到涂有脫模劑的預(yù)熱至80℃的模具中,80 ℃抽真空脫泡若干時間;最后放入烘箱中按照“80℃/2 h— l00℃/2 h”進行固化,自然冷卻后脫模,切割成標準試樣,備用。
1.3.2 復(fù)合材料的制備
以EP/固化劑/活性稀釋劑為基體、單向玻璃纖維為增強材料,制備相應(yīng)的復(fù)合材料。
1.4 測試或表征
(1)凝膠時間:采用凝膠板拉絲法進行測定(以恒定溫度時試樣由熔融抽絲至拉不出絲時的時間段,作為該溫度時的凝膠時間)。
(2)熱性能或玻璃化轉(zhuǎn)變溫度(Tg ):采用差示掃描量熱(DSC)法進行表征(試樣表面用丙酮擦拭干凈,取樣量為5 mg,升溫速率為2 K/min或10 K/min,N 氣氛)。
(3)力學(xué)性能(沖擊強度、斷裂伸長率、拉伸強度和模量):按照GB/T 2567-2008標準進行測定。
(4)短梁剪切強度:按照GB/T 1446- 005標準,采用萬能試驗機進行測定(拉伸速率為2 mm/min,23℃測定)。
(5)彎曲性能(強度、模量):按照GB/T 1449—2005標準,采用拉力試驗機進行測定(加載速率為2 mm/min.23 測定)。
(6)黏度:采用旋轉(zhuǎn)黏度計進行測定(2 #轉(zhuǎn)子,轉(zhuǎn)速為750 r/min,25℃測定)。
2 結(jié)果與討論
2.1 EP澆鑄體的放熱特性
圖1為EP澆鑄體(EP/BH一1質(zhì)量比為100:6)的DSC放熱曲線。由圖l可知:EP固化體系的反應(yīng)溫度不高,其固化反應(yīng)始于45.6℃ ,并且在87.4℃時出現(xiàn)反應(yīng)峰值;放熱曲線整體比較平緩,說明該固化體系的成型溫度選擇范圍相對較寬,并且在該溫度范圍內(nèi)固化體系的化學(xué)反應(yīng)較平緩,不會出現(xiàn)局部反應(yīng)過熱現(xiàn)象。
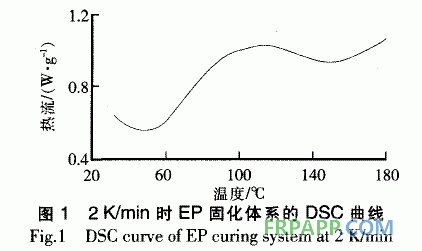
綜上所述,為加快反應(yīng)的進行,澆鑄體的固化工藝確定為“80℃/2 h一100℃/2 h”。
2.2 EP澆鑄體的固化反應(yīng)
復(fù)合材料基體的選擇,是由樹脂澆鑄體的力學(xué)性能和凝膠時間來確定的。為了解EP固化體系的反應(yīng)特性,分別測試了各配方在不同溫度時的凝膠時間,結(jié)果如圖2所示。
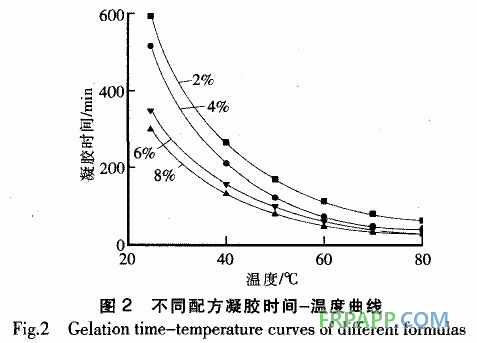
由圖2可知:隨著固化劑含量的不斷增加,各配方的凝膠時間均逐漸縮短(這是因為BH一1除具有固化劑作用外,還同時具有引發(fā)劑的作用,而引發(fā)劑含量越多,反應(yīng)速率越大,凝膠時間也就越短);對同一配方而言,固化體系的凝膠時間隨溫度升高而縮短(這是由于溫度越高分子熱運動能越大,越有利于達到反應(yīng)活化能,凝膠反應(yīng)也越易發(fā)生,并且鏈狀分子越易進一步交聯(lián)形成網(wǎng)狀大分子);各配方在80℃以上的適用期相對較短,說明此時體系的固化反應(yīng)速率對溫度較敏感;低于60℃時各配方均有較長的適用期,體系比較穩(wěn)定,這正好滿足室溫固化體系的要求(即室溫時體系比較穩(wěn)定,而較高溫度時體系反應(yīng)活性較大)。
2.3 EP澆鑄體的力學(xué)性能
各配方澆鑄體的力學(xué)性能如表1所示。由表1可知:隨著BH一1含量的不斷增加,澆鑄體的沖擊強度呈先升后降態(tài)勢,其拉伸強度和拉伸模量不斷下降,并且其彎曲強度、彎曲模量和斷裂伸長率均呈先降后升態(tài)勢。
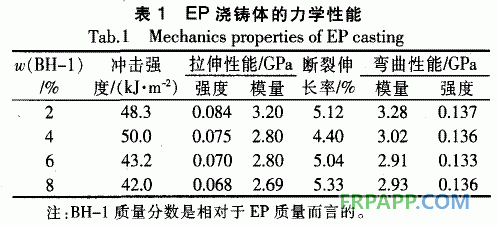
這是由于BH一1含量越高,固化反應(yīng)進行得越充分,相應(yīng)體系的力學(xué)性能越好;但是由于其兼具引發(fā)劑的作用,故BH一1(催化性固化劑)含量過高時,體系中活性點越多,分子鏈變短,尬(相對分子質(zhì)量)變小,故體系的拉伸性能越差,但韌性變好;此外,BH一1在體系中還具有降低體系黏度的作用,故體系黏度隨BH一1含量增加而降低。上述多種因素共同作用,導(dǎo)致體系力學(xué)性能隨BH一1含量不同而異;當(dāng)BH一1含量較少時,其主要起固化劑和引發(fā)劑的作用,能有效提高EP澆鑄體的力學(xué)性能;隨著BH一1含量的不斷增加,其稀釋劑作用明顯增強,并且可在較大范圍內(nèi)調(diào)節(jié)體系的黏度,有利于提高體系的綜合性能。
2.4 EP澆鑄體的
是指高分子鏈段運動剛被凍結(jié)(或被激發(fā))時的溫度。對熱固性樹脂及其復(fù)合材料結(jié)構(gòu)件而言,人們最關(guān)心的是在一定溫度下材料的強度和抗變形能力,而表征樹脂抗變形能力的最重要指標是Tg。在其他條件保持不變的前提下,EP澆鑄體的DSC曲線如圖3所示,相應(yīng)的Tg列于表2。
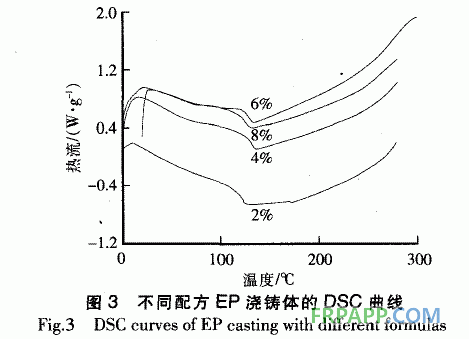
由圖3、表2可知:隨著BH一1含量的不斷增加,呈先升后降態(tài)勢,并且在較寬溫度范圍內(nèi)仍保持較高的Tg,說明不同配方在較寬溫度范圍內(nèi)均能賦予固化物較理想的耐熱性能;當(dāng) (BH一1)=4%時,體系的Tg相對最大(130.9℃)。
這是由于較多的固化劑能使反應(yīng)進行得更為完全,故固化反應(yīng)時的放熱量增大,并且反應(yīng)速率變快;當(dāng)固化劑含量過多時,體系活性點增多,高分子鏈段變短, 有所降低。
2.5 活性稀釋劑對EP澆鑄體性能的影響
在其他條件保持不變的前提下,活性稀釋劑含量對EP澆鑄體性能的影響如表3、圖4所示。由表3可知:引入活性稀釋劑后,體系的沖擊強度和 有所降低,但彎曲強度、彎曲模量、拉伸強度、拉伸模量和斷裂伸長率均有所上升。
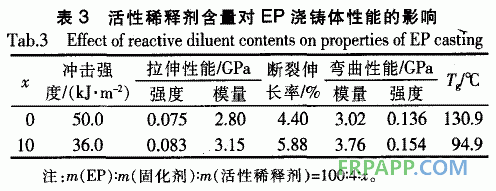
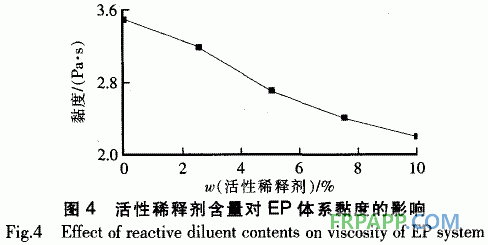
這是由于本研究采用的是單環(huán)氧基活性稀釋劑,其本身的耐熱性能不如EP/BH一1中的剛性苯環(huán)結(jié)構(gòu)。因此,引入活性稀釋劑后,體系除 降幅較大外,其他力學(xué)性能基本不變。
25℃時純EP的黏度為5~10 Pa·s 由圖4可知:體系黏度隨活性稀釋劑含量增加而降低,說明在EP/BH一1體系黏度相對較低的基礎(chǔ)上,通過改變活性稀釋劑的含量,可進一步調(diào)節(jié)體系的黏度,以滿足成型工藝對樹脂體系的黏度要求。
綜合考慮黏度等因素,本研究選擇m(EP):m(固化劑):m(活性稀釋劑)=100:4:10時較適宜。
2.6 復(fù)合材料的性能
以EP/固化劑/活性稀釋劑為基體、單向玻璃纖維為增強材料,則相應(yīng)復(fù)合材料在0。方向上的性能如表4所示。由表4可知:當(dāng)加(活性稀釋劑)=10%(相對于EP質(zhì)量而言)時,復(fù)合材料的彎曲強度、彎曲模量和層間剪切強度分別提高了26.4%、25.6%和15.2%。
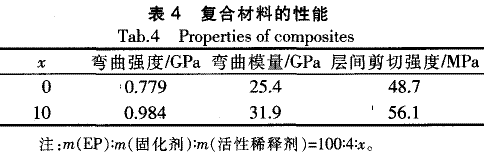
這是由于基體樹脂的黏度對復(fù)合材料性能影響較大?;钚韵♂寗┑囊虢档土嘶w樹脂的黏度,增加了基體樹脂對玻璃纖維的浸潤性, 口基體樹脂更易均勻浸潤至纖維單絲之間,同時體系中的氣泡較易排除,故復(fù)合材料的界面性能和力學(xué)性能明顯提高。
3· 結(jié)語
(1)EP/BH一1固化體系是一種室溫固化體系,其室溫凝膠時間相對較長,基本滿足大型結(jié)構(gòu)件室溫固化所需的成型固化時間要求。
(2)EP/BH一1體系的固化條件為“80℃/2 h一100℃/2 h”。當(dāng)w(BH一1)=2%或4%時,前者固化體系的拉伸強度(0.084 GPa)、彎曲模量(3.28 GPa)、彎曲強度(0.137 GPa)略優(yōu)于后者,但前者的沖擊強度(48.3 kJ/m )和 (121.4 ℃)略低于后者,并且體系的黏度調(diào)節(jié)范圍較廣。
(3)以EP/BH—l/活性稀釋劑為基體、單向玻璃纖維為增強材料,當(dāng)m(EP):m(BH一1):m(活性稀釋劑)=100:4:10時,復(fù)合材料的彎曲強度(0.984 GPa)、層間剪切強度(56.1 MPa)提高了26.4%、15.2%。
(4)BH一1是一種胺類液態(tài)催化型固化劑,其固化溫度較低,既避免了固態(tài)固化劑與EP溶解性差等缺點,又具備了胺類固化劑/EP產(chǎn)物耐熱性和力學(xué)性能俱佳等優(yōu)點。
(5)EP/BH一1/活性稀釋劑固化體系很好解決了復(fù)合材料成型技術(shù)中所面臨的室溫固化與耐高溫性能優(yōu)異、室溫固化與力學(xué)性能優(yōu)異不能同時兼顧的難題。
(6)該EP/BH一1/活性稀釋劑體系可室溫固化,并且相應(yīng)澆鑄體的力學(xué)性能和耐熱性能基本滿足大型結(jié)構(gòu)件的使用要求
環(huán)氧樹脂(EP)膠粘劑具有優(yōu)異的力學(xué)性能和粘接性能,并且其價格較低、成型工藝簡單[1-2]。EP室溫固化是節(jié)能型固化方式,在大型結(jié)構(gòu)件中具有獨 特優(yōu)勢(如不便加熱的大型結(jié)構(gòu)件的制造[3]、自然條件固化的低廉成本和優(yōu)異的力學(xué)性能等),也是廣泛應(yīng)用于國民經(jīng)濟和軍事等各領(lǐng)域中的主要原因。傳統(tǒng)EP室溫固化體系的不足之處:① 脂肪族多胺固化劑(如乙二胺、二乙烯三胺等)體系的凝膠時間過短、操作不便(有的為固體,使用時需加熱)、韌性較差且配比要求太嚴 ;② 咪唑類固化劑體系的固化時間過長,其室溫適用期為0.5~7 d;③ 叔胺類固化劑(如DMP一30)體系的室溫凝膠時間為70 min左右,難以滿足大型結(jié)構(gòu)件所需的操作期。
本研究以兼具固化劑、引發(fā)劑和稀釋劑等功能的自制BH一1為固化劑,同時引入低黏度活性稀釋劑(芐基縮水甘油醚),有望制備出一種凝膠時間約為8.5 h、配比要求不嚴、在較寬溫度范圍內(nèi)均可獲得滿意熱力學(xué)性能的EP室溫(25 ℃)固化膠粘劑。
1·試驗部分
1.1 試驗原料
環(huán)氧樹脂(EP),工業(yè)級(牌號E一5l,環(huán)氧值0.51),大連齊化化工有限公司;叔胺類固化劑(BH一1),自制;丙酮,化學(xué)純,西安化學(xué)試劑總廠;芐基縮水甘油醚(活性稀釋劑),化學(xué)純(25℃黏度5~10 mPa·S),常熟佳發(fā)化學(xué)有限責(zé)任公司。
S一玻璃纖維簾子布,南京玻璃研究設(shè)計院。
1.2 試驗儀器
CS101一lAB型電熱干燥箱,重慶銀河實驗儀器有限公司;CMT型萬能試驗機、ZBC一4型沖擊試驗機、83001 1型拉力試驗機,深圳新三思材料檢測有限公司;NDJ一79型旋轉(zhuǎn)黏度計,上海昌吉地質(zhì)儀器有限公司;2910型差示掃描量熱分析儀,美國TA公司。
1.3 試驗制備
1.3.1 EP澆鑄體的制備
將EP在80℃時抽真空脫泡若干時間,然后加入BH一1,攪拌均勻;隨后將上述物料澆鑄到涂有脫模劑的預(yù)熱至80℃的模具中,80 ℃抽真空脫泡若干時間;最后放入烘箱中按照“80℃/2 h— l00℃/2 h”進行固化,自然冷卻后脫模,切割成標準試樣,備用。
1.3.2 復(fù)合材料的制備
以EP/固化劑/活性稀釋劑為基體、單向玻璃纖維為增強材料,制備相應(yīng)的復(fù)合材料。
1.4 測試或表征
(1)凝膠時間:采用凝膠板拉絲法進行測定(以恒定溫度時試樣由熔融抽絲至拉不出絲時的時間段,作為該溫度時的凝膠時間)。
(2)熱性能或玻璃化轉(zhuǎn)變溫度(Tg ):采用差示掃描量熱(DSC)法進行表征(試樣表面用丙酮擦拭干凈,取樣量為5 mg,升溫速率為2 K/min或10 K/min,N 氣氛)。
(3)力學(xué)性能(沖擊強度、斷裂伸長率、拉伸強度和模量):按照GB/T 2567-2008標準進行測定。
(4)短梁剪切強度:按照GB/T 1446- 005標準,采用萬能試驗機進行測定(拉伸速率為2 mm/min,23℃測定)。
(5)彎曲性能(強度、模量):按照GB/T 1449—2005標準,采用拉力試驗機進行測定(加載速率為2 mm/min.23 測定)。
(6)黏度:采用旋轉(zhuǎn)黏度計進行測定(2 #轉(zhuǎn)子,轉(zhuǎn)速為750 r/min,25℃測定)。
2 結(jié)果與討論
2.1 EP澆鑄體的放熱特性
圖1為EP澆鑄體(EP/BH一1質(zhì)量比為100:6)的DSC放熱曲線。由圖l可知:EP固化體系的反應(yīng)溫度不高,其固化反應(yīng)始于45.6℃ ,并且在87.4℃時出現(xiàn)反應(yīng)峰值;放熱曲線整體比較平緩,說明該固化體系的成型溫度選擇范圍相對較寬,并且在該溫度范圍內(nèi)固化體系的化學(xué)反應(yīng)較平緩,不會出現(xiàn)局部反應(yīng)過熱現(xiàn)象。
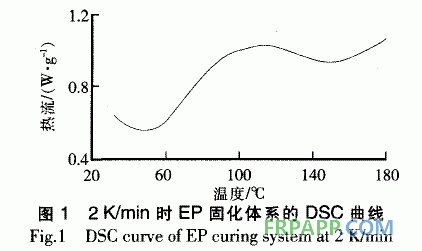
綜上所述,為加快反應(yīng)的進行,澆鑄體的固化工藝確定為“80℃/2 h一100℃/2 h”。
2.2 EP澆鑄體的固化反應(yīng)
復(fù)合材料基體的選擇,是由樹脂澆鑄體的力學(xué)性能和凝膠時間來確定的。為了解EP固化體系的反應(yīng)特性,分別測試了各配方在不同溫度時的凝膠時間,結(jié)果如圖2所示。
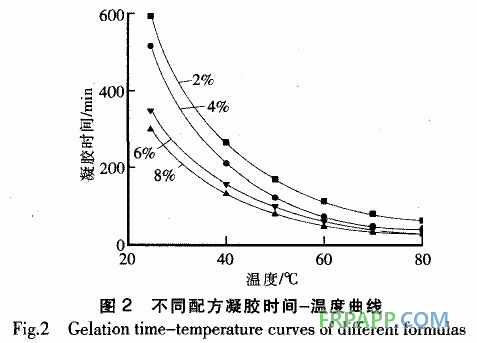
由圖2可知:隨著固化劑含量的不斷增加,各配方的凝膠時間均逐漸縮短(這是因為BH一1除具有固化劑作用外,還同時具有引發(fā)劑的作用,而引發(fā)劑含量越多,反應(yīng)速率越大,凝膠時間也就越短);對同一配方而言,固化體系的凝膠時間隨溫度升高而縮短(這是由于溫度越高分子熱運動能越大,越有利于達到反應(yīng)活化能,凝膠反應(yīng)也越易發(fā)生,并且鏈狀分子越易進一步交聯(lián)形成網(wǎng)狀大分子);各配方在80℃以上的適用期相對較短,說明此時體系的固化反應(yīng)速率對溫度較敏感;低于60℃時各配方均有較長的適用期,體系比較穩(wěn)定,這正好滿足室溫固化體系的要求(即室溫時體系比較穩(wěn)定,而較高溫度時體系反應(yīng)活性較大)。
2.3 EP澆鑄體的力學(xué)性能
各配方澆鑄體的力學(xué)性能如表1所示。由表1可知:隨著BH一1含量的不斷增加,澆鑄體的沖擊強度呈先升后降態(tài)勢,其拉伸強度和拉伸模量不斷下降,并且其彎曲強度、彎曲模量和斷裂伸長率均呈先降后升態(tài)勢。
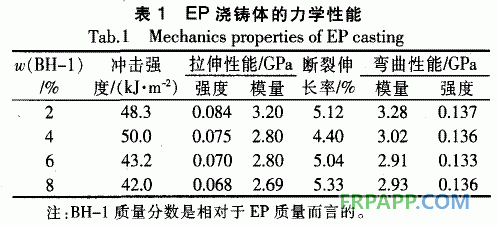
這是由于BH一1含量越高,固化反應(yīng)進行得越充分,相應(yīng)體系的力學(xué)性能越好;但是由于其兼具引發(fā)劑的作用,故BH一1(催化性固化劑)含量過高時,體系中活性點越多,分子鏈變短,尬(相對分子質(zhì)量)變小,故體系的拉伸性能越差,但韌性變好;此外,BH一1在體系中還具有降低體系黏度的作用,故體系黏度隨BH一1含量增加而降低。上述多種因素共同作用,導(dǎo)致體系力學(xué)性能隨BH一1含量不同而異;當(dāng)BH一1含量較少時,其主要起固化劑和引發(fā)劑的作用,能有效提高EP澆鑄體的力學(xué)性能;隨著BH一1含量的不斷增加,其稀釋劑作用明顯增強,并且可在較大范圍內(nèi)調(diào)節(jié)體系的黏度,有利于提高體系的綜合性能。
2.4 EP澆鑄體的
是指高分子鏈段運動剛被凍結(jié)(或被激發(fā))時的溫度。對熱固性樹脂及其復(fù)合材料結(jié)構(gòu)件而言,人們最關(guān)心的是在一定溫度下材料的強度和抗變形能力,而表征樹脂抗變形能力的最重要指標是Tg。在其他條件保持不變的前提下,EP澆鑄體的DSC曲線如圖3所示,相應(yīng)的Tg列于表2。
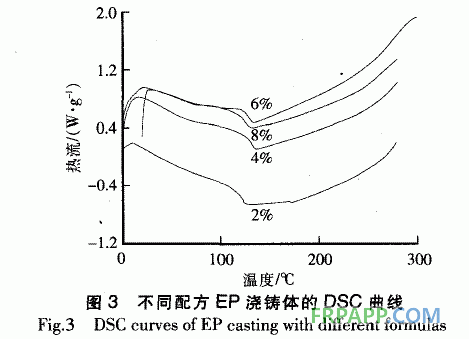
由圖3、表2可知:隨著BH一1含量的不斷增加,呈先升后降態(tài)勢,并且在較寬溫度范圍內(nèi)仍保持較高的Tg,說明不同配方在較寬溫度范圍內(nèi)均能賦予固化物較理想的耐熱性能;當(dāng) (BH一1)=4%時,體系的Tg相對最大(130.9℃)。
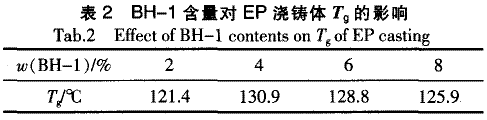
這是由于較多的固化劑能使反應(yīng)進行得更為完全,故固化反應(yīng)時的放熱量增大,并且反應(yīng)速率變快;當(dāng)固化劑含量過多時,體系活性點增多,高分子鏈段變短, 有所降低。
2.5 活性稀釋劑對EP澆鑄體性能的影響
在其他條件保持不變的前提下,活性稀釋劑含量對EP澆鑄體性能的影響如表3、圖4所示。由表3可知:引入活性稀釋劑后,體系的沖擊強度和 有所降低,但彎曲強度、彎曲模量、拉伸強度、拉伸模量和斷裂伸長率均有所上升。
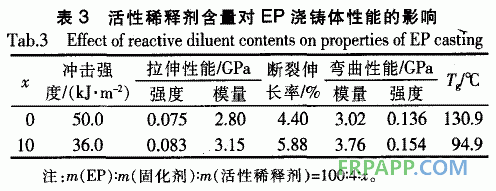
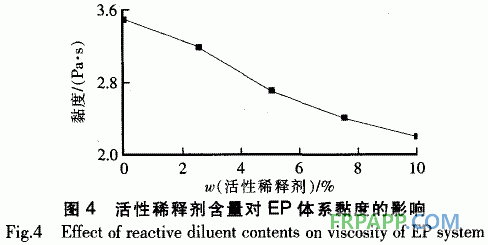
這是由于本研究采用的是單環(huán)氧基活性稀釋劑,其本身的耐熱性能不如EP/BH一1中的剛性苯環(huán)結(jié)構(gòu)。因此,引入活性稀釋劑后,體系除 降幅較大外,其他力學(xué)性能基本不變。
25℃時純EP的黏度為5~10 Pa·s 由圖4可知:體系黏度隨活性稀釋劑含量增加而降低,說明在EP/BH一1體系黏度相對較低的基礎(chǔ)上,通過改變活性稀釋劑的含量,可進一步調(diào)節(jié)體系的黏度,以滿足成型工藝對樹脂體系的黏度要求。
綜合考慮黏度等因素,本研究選擇m(EP):m(固化劑):m(活性稀釋劑)=100:4:10時較適宜。
2.6 復(fù)合材料的性能
以EP/固化劑/活性稀釋劑為基體、單向玻璃纖維為增強材料,則相應(yīng)復(fù)合材料在0。方向上的性能如表4所示。由表4可知:當(dāng)加(活性稀釋劑)=10%(相對于EP質(zhì)量而言)時,復(fù)合材料的彎曲強度、彎曲模量和層間剪切強度分別提高了26.4%、25.6%和15.2%。
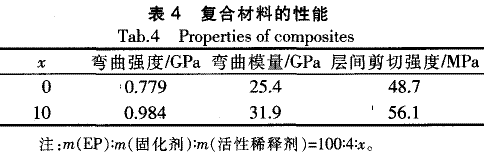
這是由于基體樹脂的黏度對復(fù)合材料性能影響較大?;钚韵♂寗┑囊虢档土嘶w樹脂的黏度,增加了基體樹脂對玻璃纖維的浸潤性, 口基體樹脂更易均勻浸潤至纖維單絲之間,同時體系中的氣泡較易排除,故復(fù)合材料的界面性能和力學(xué)性能明顯提高。
3· 結(jié)語
(1)EP/BH一1固化體系是一種室溫固化體系,其室溫凝膠時間相對較長,基本滿足大型結(jié)構(gòu)件室溫固化所需的成型固化時間要求。
(2)EP/BH一1體系的固化條件為“80℃/2 h一100℃/2 h”。當(dāng)w(BH一1)=2%或4%時,前者固化體系的拉伸強度(0.084 GPa)、彎曲模量(3.28 GPa)、彎曲強度(0.137 GPa)略優(yōu)于后者,但前者的沖擊強度(48.3 kJ/m )和 (121.4 ℃)略低于后者,并且體系的黏度調(diào)節(jié)范圍較廣。
(3)以EP/BH—l/活性稀釋劑為基體、單向玻璃纖維為增強材料,當(dāng)m(EP):m(BH一1):m(活性稀釋劑)=100:4:10時,復(fù)合材料的彎曲強度(0.984 GPa)、層間剪切強度(56.1 MPa)提高了26.4%、15.2%。
(4)BH一1是一種胺類液態(tài)催化型固化劑,其固化溫度較低,既避免了固態(tài)固化劑與EP溶解性差等缺點,又具備了胺類固化劑/EP產(chǎn)物耐熱性和力學(xué)性能俱佳等優(yōu)點。
(5)EP/BH一1/活性稀釋劑固化體系很好解決了復(fù)合材料成型技術(shù)中所面臨的室溫固化與耐高溫性能優(yōu)異、室溫固化與力學(xué)性能優(yōu)異不能同時兼顧的難題。
(6)該EP/BH一1/活性稀釋劑體系可室溫固化,并且相應(yīng)澆鑄體的力學(xué)性能和耐熱性能基本滿足大型結(jié)構(gòu)件的使用要求