1 前 言
SMC/BMC(片狀模塑料/團狀模塑料)是20世紀60年代在西德發(fā)展起來的一種新型玻璃鋼模壓材料,由于它具有輕質(zhì)高強、耐腐蝕的特點,同時具有優(yōu)良的電性能及成型工藝性,已廣泛應用于各個領域。
在制備SMC/BMC中,要得到高品質(zhì)的片材,需要控制的因素很多,但最關鍵的是樹脂糊的粘度控制,這是影響片材質(zhì)量最重要的因素。目前用于SMC/BMC的增稠劑一般有兩種:①氧化鎂;②二異氰酸酯化合物。
2 MgO增稠
通過不飽和聚酯(UP)的端羧基與氧化鎂配位形成網(wǎng)狀結(jié)構,進而使聚酯的粘度增大。這一增稠方式中,樹脂糊的粘度可以通過兩個階段進行考察和控制,即未增稠粘度增稠粘度。
2.1 樹脂未增稠粘度
樹脂糊未增稠粘度即樹脂在未加入增稠劑前的粘度,在增稠前,其粘度取決于配方中各種原材料的配比,原材料本身的粘度特性及作業(yè)環(huán)境的溫度。在配方中,由于各原材料本身的粘度不同,以不同的比例加以混合,所得到的樹脂糊粘度也各不一樣,尤其是固體原材料的加入,對粘度的影響最大。其次是同一種填料,填料的粒度和吸油值不同對粘度的影響也較大。粒度和吸油值是一對矛盾,相對來說,粒度超小,吸油值就越大,反之則相反。不同吸油值的填料對樹脂糊的粘度也有很大影響。所以在選擇填料時,除了要考慮制品本身的功能特性外,還要根據(jù)工藝的要求合理選擇一定粒度的填料。
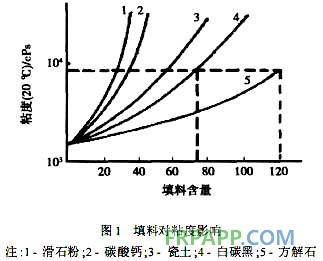
2.2 樹脂糊的增稠粘度
UP中的羧基和堿金屬氧化物發(fā)生反應生成中性鹽和水,使樹脂糊粘度大幅度上升,失去粘性,變成非粘性,這一過程叫增稠過程。在增稠反應中,堿金屬氧化物只與樹脂中的羧基發(fā)生反應,不干擾聚酯鏈和苯乙烯雙鍵,所以增稠后的樹脂不影響在制成品時的聚合反應。影響樹脂增稠的因素很多,主要包括增稠劑的用量、增稠劑本身的活性、樹脂酸值、水分含量以及環(huán)境溫度等。
據(jù)有關研究表明,樹脂的增稠是分三個分階段進行的。首先是增稠劑的擴散,使增稠劑分散于樹脂糊中;其次是增稠劑和樹脂中的羧基反應生成堿式鹽;最后堿式鹽和羧基繼續(xù)反應生成中性鹽和水。

根據(jù)增稠機理和增稠過程可知:增稠反應是一個動態(tài)平衡過程,增稠劑用量增大,增稠速度也增加,而且,如果樹脂的酸值越大,表明樹脂中羧基的濃度就越大,增稠的速度也越快。樹脂糊中微量水分對增稠粘度有極大的影響,在增稠初期,微量水分的存在起到了增稠反應的催化作用,使增稠反應速度加劇,樹脂糊粘度在短時間內(nèi)達到很高的粘度;同時,增稠反應中有水生在,如果樹脂糊中含水量較大,就會掏增稠反應,使樹脂殘留粘性,影響增稠反應的正常進行。實踐表明,樹脂糊中水分含量一般要求控制在0.15%以內(nèi)為好。
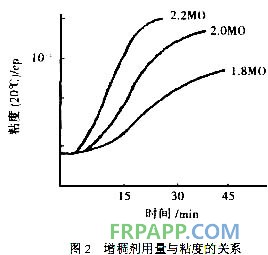
在粘度的控制當中,還有一個十分重要的因素,那就是溫度,溫度升高,使分子間的布朗運動加劇,利于增稠劑的擴散,同時提高了反應物的活化能,使增稠速度加快,樹脂糊的增稠粘度增大。在實際生產(chǎn)中,樹脂糊的溫度控制在30~35℃之間,粘度上升比較均勻,利于SMC/BMC的制備。
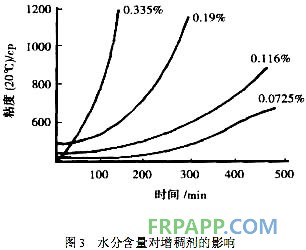
2.3 樹脂糊粘度與SMC/BMC質(zhì)量的關系
制備SMC/BMC是靠樹脂糊浸漬玻璃纖維完成的,玻纖的浸漬質(zhì)量將直接關系到片材的質(zhì)量。而玻纖的浸漬質(zhì)量除玻纖本身因素外,主要取決于樹脂糊的粘度,同時,不同的玻纖含量要求不同的粘度才能得到良好的浸漬。玻纖含量大,要求樹脂糊粘度相對要小,反之則可以適當?shù)脑龃?。所以控制樹脂糊的粘度是制備SMC/BMC的關鍵工序。
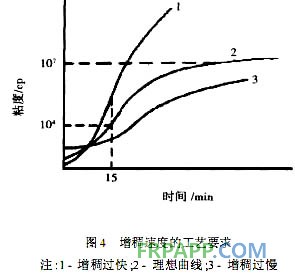
理想的增稠路線是:在片材復合的初期,要求樹脂糊的粘度相對較小,以利于玻纖的浸漬,待玻纖浸漬完全后,又要求樹脂糊的粘度迅速增大,不致于使膠液流失,并盡快的適合于模壓操作。通常情況下,在初始的15min內(nèi),樹脂糊的粘度不超過6*10(4)cp為宜。
SMC/BMC(片狀模塑料/團狀模塑料)是20世紀60年代在西德發(fā)展起來的一種新型玻璃鋼模壓材料,由于它具有輕質(zhì)高強、耐腐蝕的特點,同時具有優(yōu)良的電性能及成型工藝性,已廣泛應用于各個領域。
在制備SMC/BMC中,要得到高品質(zhì)的片材,需要控制的因素很多,但最關鍵的是樹脂糊的粘度控制,這是影響片材質(zhì)量最重要的因素。目前用于SMC/BMC的增稠劑一般有兩種:①氧化鎂;②二異氰酸酯化合物。
2 MgO增稠
通過不飽和聚酯(UP)的端羧基與氧化鎂配位形成網(wǎng)狀結(jié)構,進而使聚酯的粘度增大。這一增稠方式中,樹脂糊的粘度可以通過兩個階段進行考察和控制,即未增稠粘度增稠粘度。
2.1 樹脂未增稠粘度
樹脂糊未增稠粘度即樹脂在未加入增稠劑前的粘度,在增稠前,其粘度取決于配方中各種原材料的配比,原材料本身的粘度特性及作業(yè)環(huán)境的溫度。在配方中,由于各原材料本身的粘度不同,以不同的比例加以混合,所得到的樹脂糊粘度也各不一樣,尤其是固體原材料的加入,對粘度的影響最大。其次是同一種填料,填料的粒度和吸油值不同對粘度的影響也較大。粒度和吸油值是一對矛盾,相對來說,粒度超小,吸油值就越大,反之則相反。不同吸油值的填料對樹脂糊的粘度也有很大影響。所以在選擇填料時,除了要考慮制品本身的功能特性外,還要根據(jù)工藝的要求合理選擇一定粒度的填料。
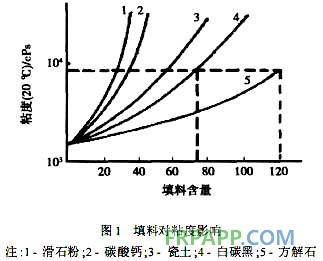
2.2 樹脂糊的增稠粘度
UP中的羧基和堿金屬氧化物發(fā)生反應生成中性鹽和水,使樹脂糊粘度大幅度上升,失去粘性,變成非粘性,這一過程叫增稠過程。在增稠反應中,堿金屬氧化物只與樹脂中的羧基發(fā)生反應,不干擾聚酯鏈和苯乙烯雙鍵,所以增稠后的樹脂不影響在制成品時的聚合反應。影響樹脂增稠的因素很多,主要包括增稠劑的用量、增稠劑本身的活性、樹脂酸值、水分含量以及環(huán)境溫度等。
1 前 言 SMC/BMC(片狀模塑料/團狀模塑料)是20世紀60年代在西德發(fā)展起來的一種新型玻璃鋼模壓材料,由于它具有輕質(zhì)高強、耐腐蝕的特點,同時具有優(yōu)良的電性能及成型工藝性,已廣泛應用于各個領域。 在制備SMC/BMC中,要得到高品質(zhì)的片材,需要控制的因素很多,但最關鍵的是樹脂糊的粘度控制,這是影響片材質(zhì)量最重要的因素。目前用于SMC/BMC的增稠劑一般有兩種:①氧化鎂;②二異氰酸酯化合物。 2 MgO增稠 通過不飽和聚酯(UP)的端羧基與氧化鎂配位形成網(wǎng)狀結(jié)構,進而使聚酯的粘度增大。這一增稠方式中,樹脂糊的粘度可以通過兩個階段進行考察和控制,即未增稠粘度增稠粘度。 2.1 樹脂未增稠粘度 樹脂糊未增稠粘度即樹脂在未加入增稠劑前的粘度,在增稠前,其粘度取決于配方中各種原材料的配比,原材料本身的粘度特性及作業(yè)環(huán)境的溫度。在配方中,由于各原材料本身的粘度不同,以不同的比例加以混合,所得到的樹脂糊粘度也各不一樣,尤其是固體原材料的加入,對粘度的影響最大。其次是同一種填料,填料的粒度和吸油值不同對粘度的影響也較大。粒度和吸油值是一對矛盾,相對來說,粒度超小,吸油值就越大,反之則相反。不同吸油值的填料對樹脂糊的粘度也有很大影響。所以在選擇填料時,除了要考慮制品本身的功能特性外,還要根據(jù)工藝的要求合理選擇一定粒度的填料。 ![]() 2.2 樹脂糊的增稠粘度 UP中的羧基和堿金屬氧化物發(fā)生反應生成中性鹽和水,使樹脂糊粘度大幅度上升,失去粘性,變成非粘性,這一過程叫增稠過程。在增稠反應中,堿金屬氧化物只與樹脂中的羧基發(fā)生反應,不干擾聚酯鏈和苯乙烯雙鍵,所以增稠后的樹脂不影響在制成品時的聚合反應。影響樹脂增稠的因素很多,主要包括增稠劑的用量、增稠劑本身的活性、樹脂酸值、水分含量以及環(huán)境溫度等。 |

根據(jù)增稠機理和增稠過程可知:增稠反應是一個動態(tài)平衡過程,增稠劑用量增大,增稠速度也增加,而且,如果樹脂的酸值越大,表明樹脂中羧基的濃度就越大,增稠的速度也越快。樹脂糊中微量水分對增稠粘度有極大的影響,在增稠初期,微量水分的存在起到了增稠反應的催化作用,使增稠反應速度加劇,樹脂糊粘度在短時間內(nèi)達到很高的粘度;同時,增稠反應中有水生在,如果樹脂糊中含水量較大,就會掏增稠反應,使樹脂殘留粘性,影響增稠反應的正常進行。實踐表明,樹脂糊中水分含量一般要求控制在0.15%以內(nèi)為好。
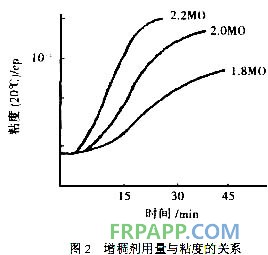
在粘度的控制當中,還有一個十分重要的因素,那就是溫度,溫度升高,使分子間的布朗運動加劇,利于增稠劑的擴散,同時提高了反應物的活化能,使增稠速度加快,樹脂糊的增稠粘度增大。在實際生產(chǎn)中,樹脂糊的溫度控制在30~35℃之間,粘度上升比較均勻,利于SMC/BMC的制備。
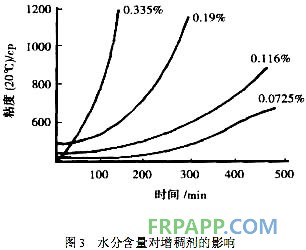
2.3 樹脂糊粘度與SMC/BMC質(zhì)量的關系
制備SMC/BMC是靠樹脂糊浸漬玻璃纖維完成的,玻纖的浸漬質(zhì)量將直接關系到片材的質(zhì)量。而玻纖的浸漬質(zhì)量除玻纖本身因素外,主要取決于樹脂糊的粘度,同時,不同的玻纖含量要求不同的粘度才能得到良好的浸漬。玻纖含量大,要求樹脂糊粘度相對要小,反之則可以適當?shù)脑龃?。所以控制樹脂糊的粘度是制備SMC/BMC的關鍵工序。
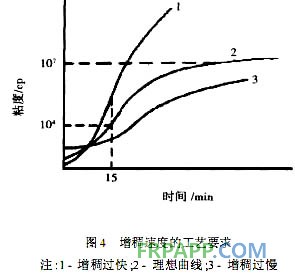
理想的增稠路線是:在片材復合的初期,要求樹脂糊的粘度相對較小,以利于玻纖的浸漬,待玻纖浸漬完全后,又要求樹脂糊的粘度迅速增大,不致于使膠液流失,并盡快的適合于模壓操作。通常情況下,在初始的15min內(nèi),樹脂糊的粘度不超過6*10(4)cp為宜。