汽車的前端模塊通常搭載前燈等大型部件,傳統(tǒng)為鋼制。新款前端模塊將框架材料由鋼換成鋁合金,并且鋁合金與樹脂使用粘合劑接合,實現(xiàn)了輕量化。與原產(chǎn)品相比,重量減輕了3.7kg,減輕了約2成(20.9%)。該粘合劑由贏創(chuàng)開發(fā)。
新款前端模塊要求實現(xiàn)能配備于實車的高設(shè)計標準。例如,低速行駛時防止變形、高速行駛時防止前發(fā)動機罩打開的耐沖擊性,以及即使被劃傷或沾上鹽水也能抑制腐蝕擴大的耐腐蝕性等,通過了嚴格的評估測試。
新款前端模塊由鋁合金框架和利用聚酰胺(PA)成型的部件構(gòu)成。從兩個部件的接合部可以看出,采用了沒有螺栓和螺母等連接件的簡單結(jié)構(gòu)。以前一直用螺絲在鋼制框架上固定樹脂部件。
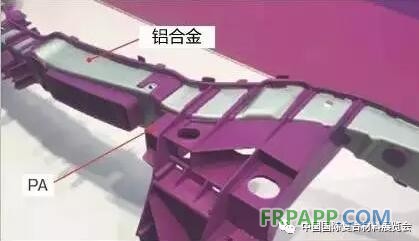
也就是說,新款前端模塊將鋼換成了鋁合金,通過粘合法省去了連接件,從而實現(xiàn)了輕量化。實現(xiàn)這一點的,是能使鋁合金與PA牢牢粘在一起的異種材料粘合劑“Vestamelt® Hylink”。此為共聚PA粘合劑,除了鋁合金外,還能粘合不銹鋼和鋼等金屬,以及PA6、PA66、PA9T、PA610、PA12等PA系樹脂。粘合原理是,金屬與粘合劑之間及粘合劑與樹脂之間都是“氫鍵和基于交聯(lián)劑的化學(xué)鍵“,粘合強度達10~20MPa。由此,前端模塊的抗扭強度達到192.2N·m,比使用其他粘合劑時(例如180.8N·m)要高。
新款前端模塊FEM的制造方法
1、靜電涂敷或卷材涂敷
首先,對鋁合金實施表面處理,去除氧化膜使表面變粗糙。這是為了提高與樹脂的粘合力。接下來,經(jīng)過脫脂處理、表面調(diào)整和干燥等各道工序后,在鋁合金表面涂敷共聚PA粘合劑。采用靜電涂敷法,用噴槍使共聚PA制粘合劑帶電,利用靜電在工件(鋁合金)表面涂敷該粘合劑。此外,還可以使用在金屬卷材上用滾輪高速涂敷該粘合劑的卷材涂敷法,作業(yè)人員也可以用刷子涂敷。利用卷材涂敷法涂敷時,有望實現(xiàn)30~50m/分鐘的高速處理。
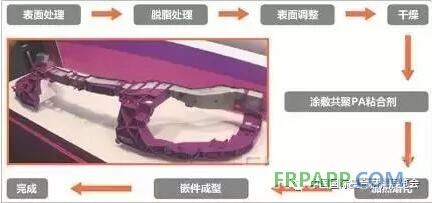
其次進入加熱熔化工序,以150~200℃的溫度對涂敷了共聚PA粘合劑的鋁合金加熱約5分鐘。粘合劑受熱后會熔化流淌。然后再進行冷卻,粘合劑就在鋁合金表面形成了厚50~150μm的膜。
2、沖壓成型
由于共聚PA粘合劑膜會牢牢粘在鋁合金表面,可以直接保管,也可以沖壓成型。因此,該粘合劑既可以在沖壓成型后的鋁合金框架上涂敷,也可以在沖壓成型前的鋁合金板上涂敷。
3、嵌件注塑成型
接下來將帶有共聚PA粘合劑膜的鋁合金放入模具,射出PA進行嵌件成型,前端模塊就完成了。成本與之前基本相同。因為省去了用螺絲連接金屬框架和樹脂部件的成本等。
儀表板橫梁CCB上的應(yīng)用
該技術(shù)已經(jīng)在儀表板的支柱——管梁上實現(xiàn)實用化。由鋁合金和PA構(gòu)成,利用共聚PA粘合劑粘合了兩種材料。戴姆勒在3款車型上采用。2013年德國戴姆勒在“梅賽德斯·奔馳A級”上首次采用,之后“梅賽德斯·奔馳B級”和“梅賽德斯·奔馳SLS級”也相繼配備。使用的PA為玻璃纖維強化PA6。重量最大減輕2成。
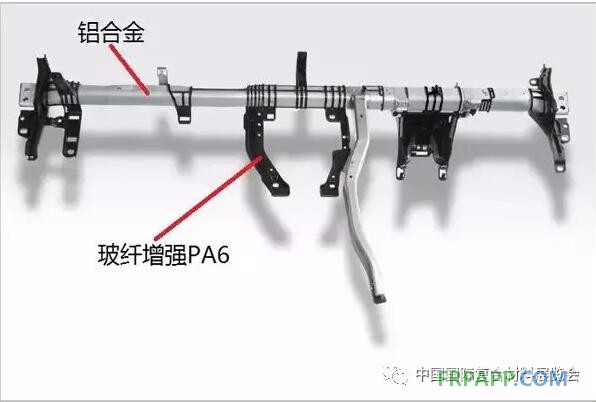